روش های کاهش آلایندگی کارخانه های سیمان
راهکارهای جامع برای صنعت سیمان سبز
صنعت سیمان به عنوان یکی از ارکان اصلی توسعه زیرساخت ها و شهرسازی نقش حیاتی در اقتصاد جهانی ایفا می کند. با این حال فرآیند تولید سیمان ذاتاً با انتشار مقادیر قابل توجهی آلاینده های زیست محیطی همراه است. این آلاینده ها شامل ذرات معلق اکسیدهای نیتروژن (NOx) اکسیدهای گوگرد (SOx) مونوکسید کربن (CO) و به ویژه دی اکسید کربن (CO2) به عنوان گاز گلخانه ای اصلی هستند.
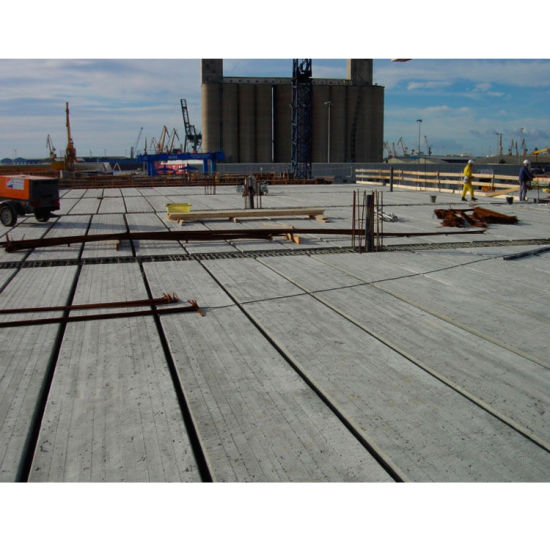
اهمیت کاهش این آلاینده ها نه تنها از منظر رعایت استانداردهای زیست محیطی و قوانین سخت گیرانه تر بلکه برای حفاظت از سلامت عمومی کاهش اثرات تغییرات اقلیمی و بهبود وجهه عمومی صنعت سیمان حیاتی است. در این مقاله تخصصی به بررسی جامع ترین و موثرترین روش ها و تکنیک های مورد استفاده در کارخانه های سیمان مدرن برای به حداقل رساندن انتشار آلاینده ها خواهیم پرداخت. هدف ما ارائه یک راهنمای کاربردی و مبتنی بر دانش روز برای متخصصان مدیران و دست اندرکاران این صنعت و علاقه مندان به مباحث محیط زیست صنعتی است.
ماهیت آلایندگی در صنعت سیمان
فرآیند تولید سیمان که عمدتاً شامل استخراج مواد اولیه (مانند سنگ آهک و خاک رس) آسیاب کردن پخت در کوره دوار با دمای بسیار بالا (حدود 1450 درجه سانتی گراد) برای تولید کلینکر و سپس آسیاب کردن کلینکر با افزودنی ها است منابع متعددی برای تولید آلاینده ها دارد. شناخت دقیق این منابع و انواع آلاینده ها اولین گام در جهت کنترل و کاهش موثر آن هاست.
انواع آلاینده های اصلی
آلاینده های منتشر شده از کارخانه های سیمان متنوع هستند و هر یک نیازمند روش های کنترلی خاص خود می باشند. مهم ترین این آلاینده ها عبارتند از:
- ذرات معلق (Particulate Matter – PM): این ذرات شامل گرد و غبار ناشی از آسیاب کردن حمل و نقل مواد و ذرات ریز خروجی از کوره و خنک کننده کلینکر هستند. ذرات معلق بزرگتر به سرعت ته نشین می شوند اما ذرات ریزتر (PM2.5 و PM10) می توانند مسافت های طولانی را طی کرده و به سلامت تنفسی آسیب برسانند.
- اکسیدهای نیتروژن (NOx): عمدتاً NO و NO2 هستند که در دمای بالای کوره سیمان از واکنش نیتروژن موجود در هوا و سوخت تشکیل می شوند (NOx حرارتی و سوختی). این گازها در تشکیل باران اسیدی و اسموگ نقش دارند.
- اکسیدهای گوگرد (SOx): عمدتاً SO2 است که از گوگرد موجود در مواد اولیه و سوخت حاصل می شود. SOx نیز عامل اصلی باران اسیدی و مشکلات تنفسی است.
- مونوکسید کربن (CO): نتیجه احتراق ناقص سوخت در کوره است. CO یک گاز سمی است.
- دی اکسید کربن (CO2): اصلی ترین گاز گلخانه ای منتشر شده در صنعت سیمان است. حدود دو سوم CO2 از کلسیناسیون سنگ آهک (تجزیه CaCO3 به CaO و CO2) و یک سوم از احتراق سوخت حاصل می شود.
- فلزات سنگین و ترکیبات آلی فرار (VOCs): ممکن است به مقادیر کم بسته به نوع مواد اولیه و سوخت منتشر شوند.
منابع تولید آلاینده ها در فرآیند سیمان
هر مرحله از فرآیند تولید سیمان می تواند منبع انتشار یک یا چند نوع آلاینده باشد:
- بخش خردایش و آسیاب مواد خام: تولید گرد و غبار.
- سیلوهای ذخیره سازی مواد خام و کلینکر: تولید گرد و غبار هنگام پر و خالی کردن.
- کوره دوار: اصلی ترین منبع انتشار NOx SOx CO CO2 و ذرات معلق ریز. دمای بالای کوره عامل اصلی تشکیل NOx و کلسیناسیون سنگ آهک عامل اصلی انتشار CO2 فرآیندی است.
- خنک کننده کلینکر: منبع مهم انتشار ذرات معلق و مقادیر کمتری NOx.
- آسیاب سیمان: تولید گرد و غبار در مرحله نهایی آسیاب کردن کلینکر با افزودنی ها.
- بسته بندی و بارگیری: تولید گرد و غبار.
تاثیرات زیست محیطی و بهداشتی آلایندگی سیمان
انتشار این آلاینده ها پیامدهای جدی برای محیط زیست و سلامت انسان دارد:
- کیفیت هوا: ذرات معلق باعث کاهش دید مشکلات تنفسی و تشدید بیماری های قلبی و ریوی می شوند. NOx و SOx در تشکیل اسموگ و باران اسیدی نقش دارند.
- آب و خاک: باران اسیدی می تواند به جنگل ها محصولات کشاورزی ساختمان ها و اکوسیستم های آبی آسیب برساند. فلزات سنگین ته نشین شده می توانند خاک و آب را آلوده کنند.
- تغییرات اقلیمی: انتشار گسترده CO2 از کارخانه های سیمان سهم قابل توجهی در افزایش غلظت این گاز در جو و تشدید اثر گلخانه ای دارد.
- سلامت انسان: تماس طولانی مدت با گرد و غبار سیمان می تواند منجر به بیماری های تنفسی مزمن مانند سیلیکوزیس شود. سایر آلاینده ها نیز اثرات منفی بر سیستم تنفسی قلبی و عصبی دارند.
روش های اولیه کاهش آلایندگی
کاهش آلایندگی در کارخانه های سیمان تنها به نصب تجهیزات پیشرفته محدود نمی شود. بسیاری از روش های موثر در دل فرآیند تولید نهفته اند و با بهینه سازی و تغییر در مواد و سوخت قابل اجرا هستند. این رویکردهای اولیه اغلب مقرون به صرفه تر بوده و می توانند به کاهش قابل توجهی در انتشار آلاینده ها منجر شوند.
بهینه سازی فرآیند تولید
بهبود راندمان فرآیند تولید سیمان به طور مستقیم بر کاهش مصرف انرژی و در نتیجه کاهش انتشار آلاینده های ناشی از احتراق تاثیر می گذارد. این بهینه سازی ها شامل موارد زیر است:
- افزایش راندمان حرارتی کوره: استفاده از پیش گرم کن ها و پیش کلسیناتورهای چند مرحله ای بهبود آب بندی کوره و خنک کننده و عایق کاری مناسب می تواند مصرف سوخت را کاهش داده و در نتیجه انتشار CO2 و NOx حرارتی را کم کند.
- کنترل دقیق فرآیند احتراق: تنظیم نسبت هوا به سوخت دمای شعله و محل تزریق سوخت می تواند به احتراق کامل تر و کاهش تولید CO و همچنین کنترل تشکیل NOx حرارتی کمک کند.
- کاهش مصرف انرژی الکتریکی: بهینه سازی عملکرد آسیاب ها و فن ها و استفاده از موتورهای با راندمان بالا مصرف برق را که خود از منابع انرژی تولیدکننده آلاینده تامین می شود کاهش می دهد.
استفاده از سوخت های جایگزین و کم آلاینده
یکی از مهم ترین استراتژی ها برای کاهش انتشار CO2 و سایر آلاینده ها جایگزینی سوخت های فسیلی سنتی (مانند زغال سنگ کک نفتی گاز طبیعی) با سوخت های جایگزین (Alternative Fuels – AF) است. این سوخت ها معمولاً از ضایعات صنعتی یا شهری با ارزش حرارتی مناسب تامین می شوند.
استفاده از AFها علاوه بر کاهش CO2 ناشی از سوخت می تواند به مدیریت پسماند نیز کمک کند. البته کنترل دقیق ورودی AFها و پایش مداوم آلاینده های خروجی برای اطمینان از عدم افزایش انتشار سایر آلاینده ها ضروری است.
استفاده از مواد اولیه جایگزین
بخشی از انتشار CO2 در صنعت سیمان ناشی از کلسیناسیون سنگ آهک است. جایگزینی بخشی از کلینکر سیمان با مواد سیمانی مکمل (Supplementary Cementitious Materials – SCMs) که نیازی به کلسیناسیون ندارند راهکار موثری برای کاهش این بخش از CO2 است.
- سرباره کوره بلند (Granulated Blast Furnace Slag – GBFS): یک محصول جانبی از صنعت فولاد است که خواص سیمانی دارد و می تواند جایگزین بخشی از کلینکر در تولید سیمان سرباره ای شود.
- خاکستر بادی (Fly Ash): محصول جانبی احتراق زغال سنگ در نیروگاه های برق است که خواص پوزولانی دارد و در تولید سیمان پوزولانی به کار می رود.
- پوزولان های طبیعی: مانند خاکستر آتشفشانی یا توف ها که دارای سیلیس و آلومین هستند و در حضور آهک و آب سخت می شوند.
- خاکستر آتشفشانی (Volcanic Ash) و توف ها (Tuffs): پوزولان های طبیعی هستند که در مناطق خاصی در دسترس اند.
استفاده از SCMs علاوه بر کاهش CO2 می تواند خواص بتن را نیز بهبود بخشد و مصرف انرژی در آسیاب سیمان را کاهش دهد زیرا SCMs معمولاً نرم تر از کلینکر هستند.
تجهیزات پیشرفته کنترل آلایندگی
در کنار بهینه سازی فرآیند نصب و نگهداری تجهیزات پیشرفته کنترل آلایندگی در نقاط کلیدی کارخانه (به ویژه دودکش کوره و خنک کننده کلینکر) برای جذب و حذف آلاینده ها قبل از انتشار در اتمسفر ضروری است.
کنترل انتشار ذرات معلق
ذرات معلق یکی از محسوس ترین آلاینده های کارخانه های سیمان هستند و کنترل آن ها از اولویت بالایی برخوردار است. تجهیزات مختلفی برای این منظور به کار می روند:
الکتروفیلترها (Electrostatic Precipitators – ESP)
ESPها با استفاده از میدان الکتریکی ذرات غبار را باردار کرده و سپس آن ها را روی صفحات جمع آوری جذب می کنند. این سیستم ها برای حجم بالای گاز و دماهای بالا مناسب هستند اما نسبت به تغییرات در خواص گاز یا ذرات حساسیت دارند.
بگ فیلترها (Bag Filters/Fabric Filters)
بگ فیلترها با عبور گازهای آلوده از کیسه های پارچه ای ذرات غبار را به روش مکانیکی فیلتر می کنند. این روش بسیار موثر است و می تواند راندمان جمع آوری ذرات بسیار بالایی (بیش از 99.9%) داشته باشد. بگ فیلترها به دما و رطوبت گاز حساس هستند و نیاز به تمیز کردن منظم کیسه ها دارند.
سیکلون ها و مولتی سیکلون ها (Cyclones and Multi-cyclones)
این تجهیزات با استفاده از نیروی گریز از مرکز ذرات بزرگتر را از جریان گاز جدا می کنند. سیکلون ها معمولاً به عنوان پیش فیلتر قبل از ESP یا بگ فیلتر برای کاهش بار غبار ورودی به سیستم اصلی استفاده می شوند.
کنترل انتشار گازهای آلاینده
کنترل گازهای آلاینده مانند NOx SOx و CO2 نیازمند روش های شیمیایی یا فیزیکی پیچیده تری است.
کنترل اکسیدهای نیتروژن (NOx)
روش های کنترل NOx به دو دسته اصلی تقسیم می شوند:
روش های اولیه (Primary Methods)
این روش ها با هدف کاهش تشکیل NOx در داخل کوره اجرا می شوند:
- احتراق مرحله ای (Staged Combustion): با تقسیم تزریق هوا به دو یا چند مرحله دمای شعله کاهش یافته و تشکیل NOx حرارتی کمتر می شود.
- استفاده از مشعل های کم NOx (Low-NOx Burners): این مشعل ها با کنترل دقیق اختلاط سوخت و هوا شعله ای با دمای پایین تر و توزیع حرارت متفاوت ایجاد می کنند.
- تزریق سوخت به نقاط مختلف کوره: تغییر محل تزریق سوخت می تواند بر پروفیل دمایی کوره و تشکیل NOx تاثیر بگذارد.
روش های ثانویه (Secondary Methods)
این روش ها با هدف حذف NOx از گازهای خروجی پس از تشکیل آن ها در کوره اجرا می شوند:
- کاهش غیرانتخابی کاتالیستی (Non-Selective Catalytic Reduction – NSCR): استفاده از کاتالیست برای کاهش NOx به N2 در حضور CO و هیدروکربن ها. کمتر رایج در سیمان.
- کاهش غیرانتخابی غیرکاتالیستی (Non-Selective Non-Catalytic Reduction – NSNCR): تزریق سوخت اضافی به ناحیه ای با دمای بالا در مسیر گازهای خروجی (مانند رایزر داون کامر) برای کاهش NOx.
- کاهش انتخابی غیرکاتالیستی (Selective Non-Catalytic Reduction – SNCR): تزریق عامل کاهنده (مانند آمونیاک یا اوره) به ناحیه ای با دمای مناسب (حدود 850-1100 درجه سانتی گراد) در کوره یا پیش گرم کن برای واکنش با NOx و تبدیل آن به N2 و H2O.
- کاهش انتخابی کاتالیستی (Selective Catalytic Reduction – SCR): تزریق عامل کاهنده (آمونیاک یا اوره) به گازهای خروجی در دمای پایین تر (حدود 250-450 درجه سانتی گراد) در حضور یک کاتالیست. این روش بسیار موثر است اما هزینه برتر است و نیاز به نصب راکتور کاتالیستی دارد.
انتخاب بین SNCR و SCR بستگی به سطح مورد نیاز کاهش NOx و ملاحظات اقتصادی دارد. SNCR معمولاً ساده تر و ارزان تر است اما راندمان کمتری نسبت به SCR دارد.
کنترل اکسیدهای گوگرد (SOx)
SOx عمدتاً از گوگرد موجود در مواد اولیه و سوخت حاصل می شود. بخش قابل توجهی از SO2 در داخل کوره توسط آهک آزاد (CaO) موجود در کلینکر جذب می شود. با این حال اگر میزان گوگرد بالا باشد یا جذب داخلی کافی نباشد نیاز به روش های کنترلی اضافی است.
روش های جذب خشک و نیمه خشک (Dry and Semi-dry Scrubbing)
تزریق جاذب های پودری یا دوغاب آهک/سنگ آهک به جریان گازهای خروجی برای واکنش با SO2 و تشکیل سولفات کلسیم. این روش ها معمولاً قبل از بگ فیلتر نصب می شوند تا ذرات جاذب واکنش داده و نداده توسط فیلتر جمع آوری شوند.
روش های جذب مرطوب (Wet Scrubbing)
عبور گازهای خروجی از برجی که در آن با دوغاب جاذب (معمولاً سنگ آهک یا آهک) تماس داده می شوند. SO2 در دوغاب جذب شده و محصول جانبی (مانند گچ) تولید می شود. این روش بسیار موثر است اما نیاز به مدیریت پساب دارد.
کنترل دی اکسید کربن (CO2) و گازهای گلخانه ای
کاهش CO2 بزرگترین چالش زیست محیطی صنعت سیمان است. روش های کنترل CO2 شامل:
جذب کربن (Carbon Capture)
فناوری هایی که CO2 را از گازهای خروجی کارخانه جدا می کنند. این فناوری ها هنوز در صنعت سیمان در مراحل اولیه توسعه یا پایلوت هستند و شامل جذب شیمیایی جذب فیزیکی جداسازی غشایی یا استفاده از حلقه های کربناتی می شوند. CO2 جذب شده می تواند ذخیره (Carbon Capture and Storage – CCS) یا استفاده مجدد (Carbon Capture and Utilization – CCU) شود.
افزایش بهره وری انرژی
همانطور که پیشتر ذکر شد کاهش مصرف سوخت از طریق بهینه سازی فرآیند و استفاده از فناوری های جدید به طور مستقیم انتشار CO2 ناشی از احتراق را کاهش می دهد.
استفاده از SCMs و سیمان های با کلینکر کمتر
جایگزینی بخشی از کلینکر با مواد سیمانی مکمل به طور مستقیم انتشار CO2 ناشی از کلسیناسیون را کاهش می دهد. توسعه و استفاده از سیمان های جدید با نسبت کلینکر بهینه یا حتی سیمان های غیرکلینکری نیز در این راستا اهمیت دارد.
کنترل سایر آلاینده ها
کنترل CO معمولاً با اطمینان از احتراق کامل در کوره و پایش مداوم محتوای CO در گازهای خروجی انجام می شود. فلزات سنگین و VOCs نیز با کنترل دقیق مواد اولیه و سوخت های جایگزین و استفاده از فیلترهای مناسب تا حدی کنترل می شوند.
نقش مدیریت و فناوری در کاهش آلایندگی
پیاده سازی موفق روش های کاهش آلایندگی نیازمند رویکردی جامع است که شامل جنبه های مدیریتی پایش مستمر نگهداری موثر و سرمایه گذاری در فناوری های نوین باشد.
پایش و اندازه گیری مستمر
نصب سیستم های پایش پیوسته انتشار (Continuous Emission Monitoring Systems – CEMS) در دودکش اصلی کارخانه برای اندازه گیری غلظت آلاینده هایی مانند ذرات معلق NOx SOx CO و O2 (برای محاسبه دبی جرمی) ضروری است. این سیستم ها امکان ارزیابی لحظه ای عملکرد تجهیزات کنترلی شناسایی مشکلات فرآیندی و اطمینان از رعایت استانداردها را فراهم می کنند.
نگهداری و بهسازی تجهیزات
عملکرد صحیح و موثر تجهیزات کنترل آلایندگی به شدت وابسته به نگهداری منظم و تخصصی آن هاست. برنامه های نگهداری پیشگیرانه بازرسی های دوره ای و تعمیرات به موقع برای اطمینان از راندمان بالای فیلترها اسکرابرها و سیستم های تزریق مواد کاهنده حیاتی هستند. بهسازی و ارتقاء تجهیزات قدیمی نیز می تواند به بهبود قابل توجهی در عملکرد زیست محیطی منجر شود.
نوآوری و تحقیق و توسعه
صنعت سیمان به طور فزاینده ای در حال سرمایه گذاری بر روی تحقیق و توسعه برای یافتن راهکارهای نوآورانه جهت کاهش آلایندگی به ویژه CO2 است. این شامل توسعه سیمان های جدید با ردپای کربن کمتر فناوری های پیشرفته جذب کربن و استفاده از انرژی های تجدیدپذیر در فرآیند تولید است.
استانداردها قوانین و مشوق ها
استانداردهای انتشار آلاینده ها که توسط سازمان های حفاظت محیط زیست ملی و بین المللی تعیین می شوند نقش محرکی در وادار کردن کارخانه ها به سرمایه گذاری در فناوری های کنترلی دارند. قوانین سخت گیرانه تر و همچنین مشوق های دولتی (مانند اعتبارات مالیاتی یا تسهیلات برای سرمایه گذاری های سبز) می توانند فرآیند پذیرش فناوری های کاهش آلایندگی را تسریع کنند.
چالش ها و فرصت ها در کاهش آلایندگی صنعت سیمان
گرچه روش های موثری برای کاهش آلایندگی در صنعت سیمان وجود دارد اما پیاده سازی آن ها با چالش هایی نیز همراه است. در عین حال این تلاش ها فرصت های جدیدی را نیز ایجاد می کنند.
چالش های فنی و اقتصادی
- هزینه بالای سرمایه گذاری: نصب تجهیزات پیشرفته کنترل آلایندگی مانند SCR یا سیستم های جذب کربن نیازمند سرمایه گذاری اولیه بسیار زیادی است.
- هزینه های عملیاتی و نگهداری: این تجهیزات نیاز به مصرف انرژی مواد شیمیایی و نگهداری تخصصی دارند که هزینه های عملیاتی را افزایش می دهد.
- پیچیدگی فنی: ادغام فناوری های جدید با فرآیندهای موجود و آموزش پرسنل برای بهره برداری و نگهداری آن ها می تواند چالش برانگیز باشد.
- در دسترس بودن و کیفیت سوخت ها و مواد اولیه جایگزین: تامین پایدار و با کیفیت سوخت ها و مواد اولیه جایگزین در همه مناطق ممکن نیست و نیازمند زیرساخت های جمع آوری و آماده سازی است.
فرصت های بهبود و توسعه پایدار
- افزایش بهره وری منابع: استفاده از سوخت ها و مواد اولیه جایگزین به ویژه ضایعات به کاهش مصرف منابع طبیعی و مدیریت پسماند کمک می کند.
- بهبود وجهه و مسئولیت اجتماعی شرکت: سرمایه گذاری در کاهش آلایندگی می تواند اعتبار شرکت را افزایش داده و مسئولیت اجتماعی آن را نشان دهد.
- نوآوری و مزیت رقابتی: پیشگامی در پذیرش فناوری های سبز می تواند منجر به کسب مزیت رقابتی در بازارهای آینده شود که به محصولات با ردپای کربن کمتر اهمیت می دهند.
- ایجاد بازارهای جدید: توسعه فناوری های جذب کربن و استفاده از CO2 جذب شده می تواند بازارهای جدیدی را برای محصولات و خدمات مرتبط ایجاد کند.
سوالات متداول (FAQ)
موثرترین روش برای کنترل گرد و غبار در کارخانه های سیمان چیست؟
بگ فیلترها (فیلترهای کیسه ای) به طور کلی به عنوان موثرترین تجهیزات برای جمع آوری ذرات معلق ریز در کارخانه های سیمان شناخته می شوند و می توانند راندمان جمع آوری بسیار بالایی داشته باشند.
چگونه استفاده از سوخت های جایگزین به کاهش آلایندگی CO2 کمک می کند؟
استفاده از سوخت های جایگزین که اغلب از منابع زیستی یا ضایعات با کربن خنثی (مانند بیومس) یا با کربن کمتر از سوخت های فسیلی سنتی هستند باعث کاهش انتشار خالص CO2 ناشی از احتراق می شود.
آیا فناوری جذب کربن در صنعت سیمان در حال حاضر کاربردی است؟
فناوری جذب کربن برای صنعت سیمان در حال توسعه و آزمایش در مقیاس پایلوت است و هنوز به طور گسترده در کارخانه ها پیاده سازی نشده اما پتانسیل بالایی برای کاهش قابل توجه انتشار CO2 دارد.
تفاوت اصلی بین روش های SNCR و SCR برای کنترل NOx چیست؟
تفاوت اصلی در وجود کاتالیست است. SCR از کاتالیست برای انجام واکنش کاهش NOx در دمای پایین تر استفاده می کند که منجر به راندمان بالاتری نسبت به SNCR می شود که بدون کاتالیست و در دمای بالاتر عمل می کند.
استانداردهای زیست محیطی چه نقشی در کاهش آلایندگی کارخانه های سیمان دارند؟
استانداردها و قوانین زیست محیطی الزامات قانونی را برای حداکثر میزان مجاز انتشار آلاینده ها تعیین می کنند و کارخانه ها را وادار به سرمایه گذاری و استفاده از فناوری ها و روش های کنترلی مناسب برای رعایت این حدود می کنند.
آیا شما به دنبال کسب اطلاعات بیشتر در مورد "روش های کاهش آلایندگی کارخانه های سیمان" هستید؟ با کلیک بر روی اقتصادی, کسب و کار ایرانی، ممکن است در این موضوع، مطالب مرتبط دیگری هم وجود داشته باشد. برای کشف آن ها، به دنبال دسته بندی های مرتبط بگردید. همچنین، ممکن است در این دسته بندی، سریال ها، فیلم ها، کتاب ها و مقالات مفیدی نیز برای شما قرار داشته باشند. بنابراین، همین حالا برای کشف دنیای جذاب و گسترده ی محتواهای مرتبط با "روش های کاهش آلایندگی کارخانه های سیمان"، کلیک کنید.